
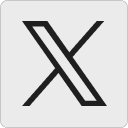


If we have learned anything from the Covid pandemic, it is that Supply Chains are forever encountering disruptions. Single sourcing, (while a great strategy for cost containment), is only as strong as its weakest link and when one link is weakened or broken, businesses are left with no options.
Global Supply chains depend upon the local environment and local economies of their supply sources, with no or very little control. For example, companies are finally starting to show some real concern about China and their Zero-Covid shutdown policies and its impact on production. The Foxconn iPhone city in Zhengzhou employees more than 200,000 people. According to Barrons, protests, quarantines and worker exodus are delaying the manufacture of 15 million smartphones and could cost Apple as much as $8 billion in the current quarter alone.
This is clearly becoming an issue of Supply Chain resilience vs ability to deliver product as companies realize long distance-low-cost labor sourcing comes with a price. Therefore, we believe more and more companies will look to move their Supply Chain closer to the end consumer with fewer intermediary parts.
China is no longer the low-cost production option it was in years past, as wages have increased dramatically in recent years. So, are the rumors true about Apple? Will companies look to shift production to other Southeast Asia countries, like India?
According to the Wall Street Journal, China exports are falling at the steepest rate in 2 years with exports to the US down 25% year-over-year while US Apparel imports from Vietnam are up 16% with China only up 4.9%. We believe Apple will be forced to move at least some production away from China, in the near future.
Multi-Sourcing and Inventory Management
Single sourcing, long the policy of lowering costs is coming with a cost of its own, Reliability. In an earlier blog, we talked about inventory shortages, with companies needing to shift from “Just-in-Time” to “Just in Case” to secure enough inventory to maintain production levels and maintain an adequate quantity of product or face the loss of sales. This shift of moving away from Single Sourcing will require companies to developing options, and contingency plans, that assure their supply chains are not only strong, but also very flexible and fluid.
As an example, airplane production is falling short of completion due to delays in delivering parts. With travel surging again, demand is up while manufacturers struggle to ship their products.
The same is true in the auto manufacturing sector. Inventory shortages are mounting, causing lost sales. Recently, a friend went to purchase a new car and was told of a 2 year wait, so he settled for a lesser model and recently took delivery. His choice of course, but what if you don’t want a lesser model, is your only option to just wait it out?
North America is the most internationally focused and least home sourced region in the world, getting the greatest percentage of its goods from Asia-Pacific countries, while the Asia-Pacific region has been hardest hit by shipping complications. Delays in obtaining raw materials and delays in shipping are causing the greatest slowdowns in production of and delivery of finished goods. These 2 factors alone will cause companies to consider reshoring as they shift from cost to reliability. But now the issue becomes finding reliable partners within your region.
What to do
With all the troubles in the world, will US Companies begin to think it just might be more economical to return sourcing and manufacturing to US soil?
“With labor rates in China doubling over the past few years, companies are now considering moving back to America” says Rosemary Coates, Executive Director, Reshoring Institute.
This sounds great and answers our original question. YES, now just might be the right time to take things seriously and make the hard decisions before it is too late?”
The head of one of the world’s largest logistics operators believes the supply-chain turmoil of the past two years is a prelude to deeper, long-lasting changes in trade patterns. Marie-Christine Lombard, president of France-based freight-forwarder Geodis, told the Wall Street Journal Logistics Report’s Paul Berger that globalization isn’t so much retreating as it is changing, with companies turning away from a single-minded push into China as they search for resilient operations. The shift began before the Covid pandemic but has accelerated more recently, Ms. Lombard says, driving greater complexity in how goods are manufactured and distributed. Companies are looking to move away from depending on a single country to source goods, she says, a strategy that demands that logistics operators manage flows between a wider range of origins and destinations. One hurdle remains, the infrastructure in developing markets that lags behind the ports and highways in long-established supply chains.
For America to regain its manufacturing prowess, we will need to automate production, redesign processes and extract labor costs. In other words, rethink:
- Where to manufacture?
- What to manufacture?
- How to manufacture?
- Who to manufacture with (source & supply chain partners)?
- And how much inventory to hold?
Companies can no longer depend totally on China and single source their Supply Chain needs. They will need options and multiple sources of suppliers; they will need to be agile and well prepared for delivery delays, parts shortages and must build contingency plans that take into account unexpected interruptions.
At ICC, we expect the unexpected. We are with you every step of the way. We plan for interruptions and build in contingencies so you get your deliveries on time and on budget.

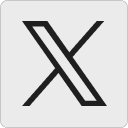

